The company SKIF TG has completed a large-scale project for the reconstruction of aspiration systems at the elevator of TRANSPED s.r.o. The work was carried out within tight deadlines and under challenging conditions, further confirming the high level of professionalism of the company's specialists.
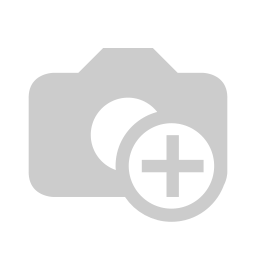
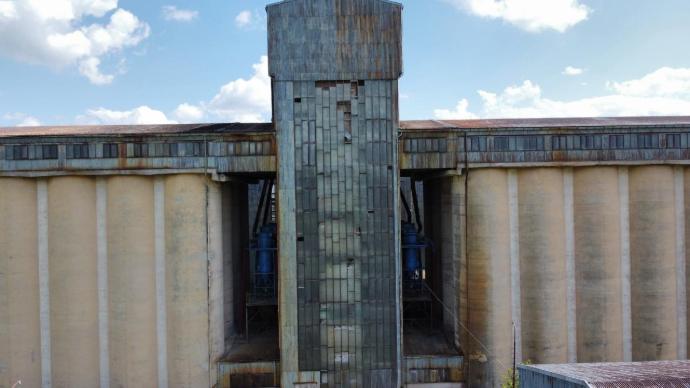
Project Facts and Results:
The client approached SKIF TG with a problem of insufficient efficiency of the existing aspiration systems. The engineering department proposed two possible solutions:
- Installation of local filters at the filling points.
- Repair of the existing systems with the replacement of dust collection equipment.
After careful analysis, the second option was chosen, as it provided more reliable operation and met the client's economic requirements.
The main challenges of the reconstruction included limited space, the inability to use standard lifting equipment, and physical wear of the supporting metal structures. For successful installation, the SKIF TG specialists disassembled all filter housings into separate components, and the installation was carried out in layers, starting with the installation of support frames and ending with the staged assembly of the filter housings.
Thanks to the coordinated work of the engineers and the assembly department of the client's service, the entire equipment and ductwork components were replaced within three months.
This project was a serious test for our team, but thanks to the experience and high qualifications of our specialists, we successfully completed the task. Measurement results confirmed the high efficiency of the modernized system – emissions into the environment did not exceed 10 mg/m³. This is an impressive result that we are proud of.
The reconstruction of the aspiration systems at the TRANSPED s.r.o. elevator became successful project for SKIF TG. The company continues to demonstrate high work standards, offering clients effective and innovative solutions. Thanks to the accumulated knowledge and experience, the SKIF TG team is always ready for new challenges and complex technical tasks.

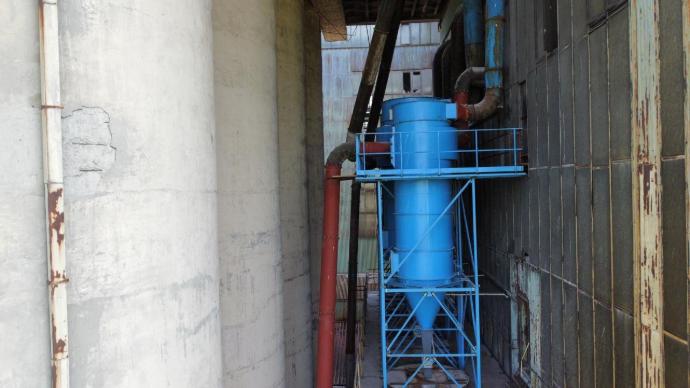